
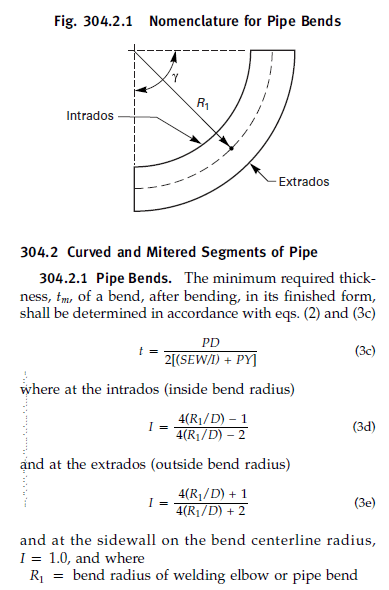

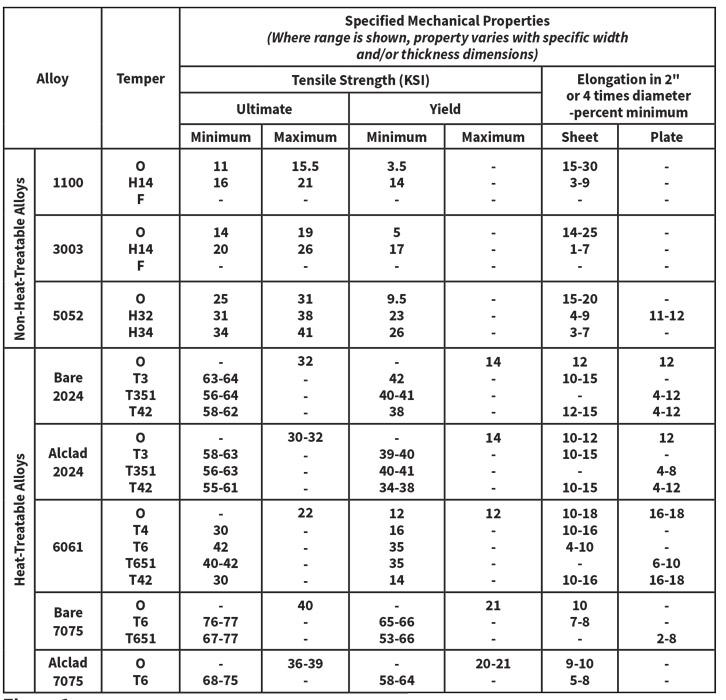
Connectors on ESD sensitive hardware shall be protected by ESD rated dust caps/covers. The mating surfaces of all unmated connectors shall be protected by covers during storage, handling and installation. Connector cable clamps and cable straps are properly set. Harnesses exhibit a neatly organized layout with smooth bends and sufficient stress relief. The use of right-angle connectors shall be minimized and restricted to applications where stress-free mounting of the cable assembly can be assured. Harnesses should be designed so that coaxial/fiber optic cables are located at or near the bundle center to minimize flexure and to provide additional protection.Ĭoaxial cable (flexible, semi-rigid, rigid) and fiber optic cables shall exhibit a neatly organized layout, with smooth bends and sufficient stress relief.Ĭonnectors shall be straight, right-angle or flange-mount. Often the most overlooked and ignored component of any electrical/electronic design, cable and harnesses are essential to the accurate and rapid transmission of data and control signals.Ĭonnector backshells shall be potted and molded, or use stress relief boots as required, in accordance with applicable engineering documentation.Ĭables and harnesses shall not be subjected to bending forces resulting in radii less than the minimum specified for the most sensitive component (i.e.: coaxial, fiber, etc.) in the assembly. Tabs must be at least 2 times the material’s thickness or 0.126”, whichever is greater, and can be no longer than 5 times its width.CABLE AND HARNESS GENERAL REQUIREMENTS CABLE AND HARNESS Notches must be at least the material’s thickness or 0.04”, whichever is greater, and can be no longer than 5 times its width. Recommended corner radius for notches should be 0.5 * t. Recommendations for Notch Feature: Notch width should not be narrower than 1.5 * t. Tabs must have a minimum distance from each other of 1mm or the material’s thickness, whichever is greater. For bends, notches must be at least 3 times the material’s thickness plus the bend radius. Notches must be at least 3.175mm away from each other. Notching is a low-cost process, particularly for its low tooling costs with a small range of standard punches. To avoid such condition notch should be placed at appropriate distance from bend with respect to sheet thickness. In case, distance between the notches to bend is very small then distortion of sheet metal may take place. Notching is a shearing operation that removes a section from the outer edge of the metal strip or part.
